
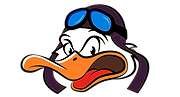
RUPTURED DUCK LLC


COMPOSIT CONSUMABLES

Vacuum Bagging Films
Vacuum Bagging Films are used to seal and provide even pressure to the laminate and tooling surface. Vacuum is applied to ensure compaction, minimize voids and the removal of volatiles. Vacuum Bagging Film should be of a high quality, and possess characteristics such as, resistance to tearing, high modulus, high elongation, resistance to“pin holing” and high temperature resistance. Components, particularly with complex geometries, must
be vacuum bagged with plenty of tucks to give ‘depth’ to the film.
Vacuum Bagging Films
-
Application of compaction pressure to consolidate plies and minimize voids
-
Extraction of moisture, solvents, and volatiles
-
Allow resin to flow and be abs

ADVANTAGES
The advantages of vacuum bagging are multi-fold and can be identified both structurally and economically. First and most important, vacuum bagging provides equal pressure to all surfaces of the part, whether the part is made up of vertical, horizontal, curved, compound curved or any combination of these. The only limit on the complexity of the part to be bagged is the extent of the planning on the part of the person performing the lay-up process. A uniform external positive pressure and negative internal pressure will aid in expelling air trapped between the core and the laminate thus limiting the possibility of “voids” in the structure.
VACCUM BAGGING
Breather Cloth
Breather Cloth is a material, which will not compress under pressure to the extent that air cannot be drawn through it. Often, an otherwise perfectly sealed bag will not develop full vacuum pressure because the bag under the hose fitting is pinched off preventing evacuation of air from the rest of the part.

ADVANTAGES
The advantages of vacuum bagging are multi-fold and can be identified both structurally and economically. First and most important, vacuum bagging provides equal pressure to all surfaces of the part, whether the part is made up of vertical, horizontal, curved, compound curved or any combination of these. The only limit on the complexity of the part to be bagged is the extent of the planning on the part of the person performing the lay-up process. A uniform external positive pressure and negative internal pressure will aid in expelling air trapped between the core and the laminate thus limiting the possibility of “voids” in the structure.
Breather Cloth
sealant tapes
Sealant tapes are used to seal the bagging film to the tool or part. They are very pliable and similar in texture to “chewing gum”. Most sealant tapes are butyl-based material which will stick to most bagging films (except silicone which is self-sealing) and to most fiberglass, aluminum, and plate glass tools. Sealant tapes should be tacky enough to allow for ease of sealing while maintain the vacuum bag able to remove cleanly from the part or tool.

sealant
tape
BMS1-68 Grade Form II/III
BMS1-68 Grade A Form II/III is specified for the aerospace manufacturing/repair industries as a floor decking seal, thermal insulation, bulkhead backing and noise and vibration dampening pad and meets FAR 25.853 requirement as per manufacturers SRM & CMM manuals.

BMS1-68 Grade Form II/III
AWT654 Release Films
AWT654 is a high quality release film specifically designed for composite manufacturing/repair processes where elevated temperatures and pressures are required. AWT654 is manufactured to the highest quality standard to ensure outstanding chemical resistant, high thermal stability. AWT654 has excellent heat stability and has a long term temperature rating up to 400F° for standard cure cycles.
